Diseño de Correa
CDI desarrolló una gran cantidad de datos de pruebas, experiencia en proyectos y capacidad de análisis durante 30 años. Nuestras áreas de experiencia en análisis y pruebas de correas transportadoras se enumeran a continuación. Estas tecnologías se utilizan en el diseño para lograr un diseño optimo, para encontrar la causa raíz de la falla y también asistir en mejoras a sistemas existentes.
Prueba y análisis de empalme de correa
CDI realiza el diseño, análisis, prueba e inspección de empalmes. Durante la inspección de empalme, la cubierta de goma se retira con cuidado para exponer los cables de acero subyacentes. La rectitud y el diseño de los cables de acero se verifican contra la especificación de empalme. Estudiamos si hay huecos en el caucho entre los cables de acero, si hay goma que pierde adherencia en los cables de acero e intentamos determinar las ubicaciones del punto de inicio de la falla y su trayectoria de propagación.
Podemos probar muestras de empalme de correas de acero y tela para medir la resistencia estática y la resistencia a la fatiga dinámica en una máquina de prueba de tracción.
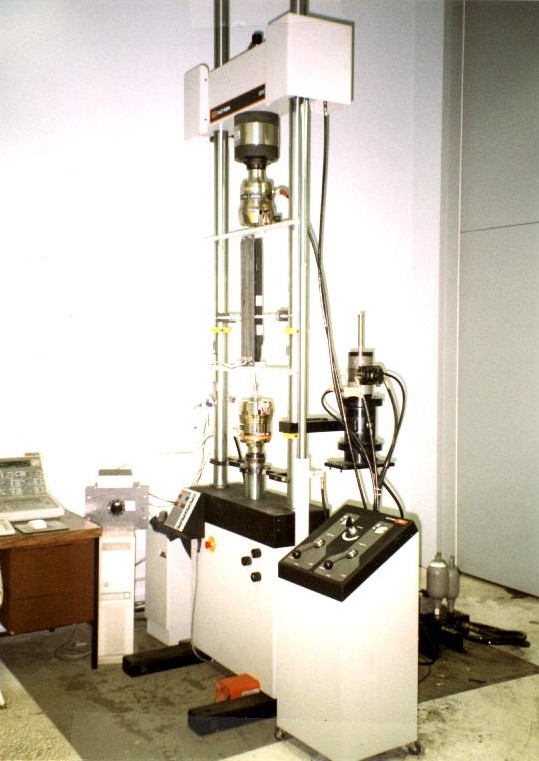
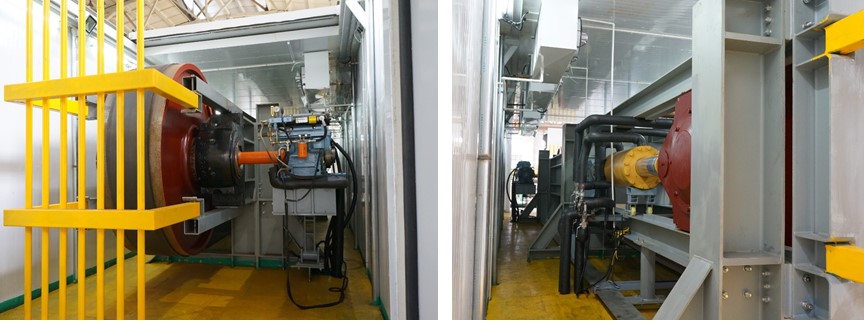
CDI desarrolló un programa de análisis de elementos finitos para analizar el esfuerzo cortante de goma en el empalme. En la figura siguiente, las áreas roja y azul (valores positivos y negativos) muestran el esfuerzo cortante de goma en dos direcciones de corte diferentes entre los cables de acero (columnas blancas), en un empalme de 3 pasos. Este programa se utiliza para optimizar los diseños de empalme cambiando el espacio de goma, la longitud del escalón y el patrón de empalme para minimizar el esfuerzo de corte. También se utiliza en el análisis de fallas de empalme de correa para investigar el nivel de tensión de corte.
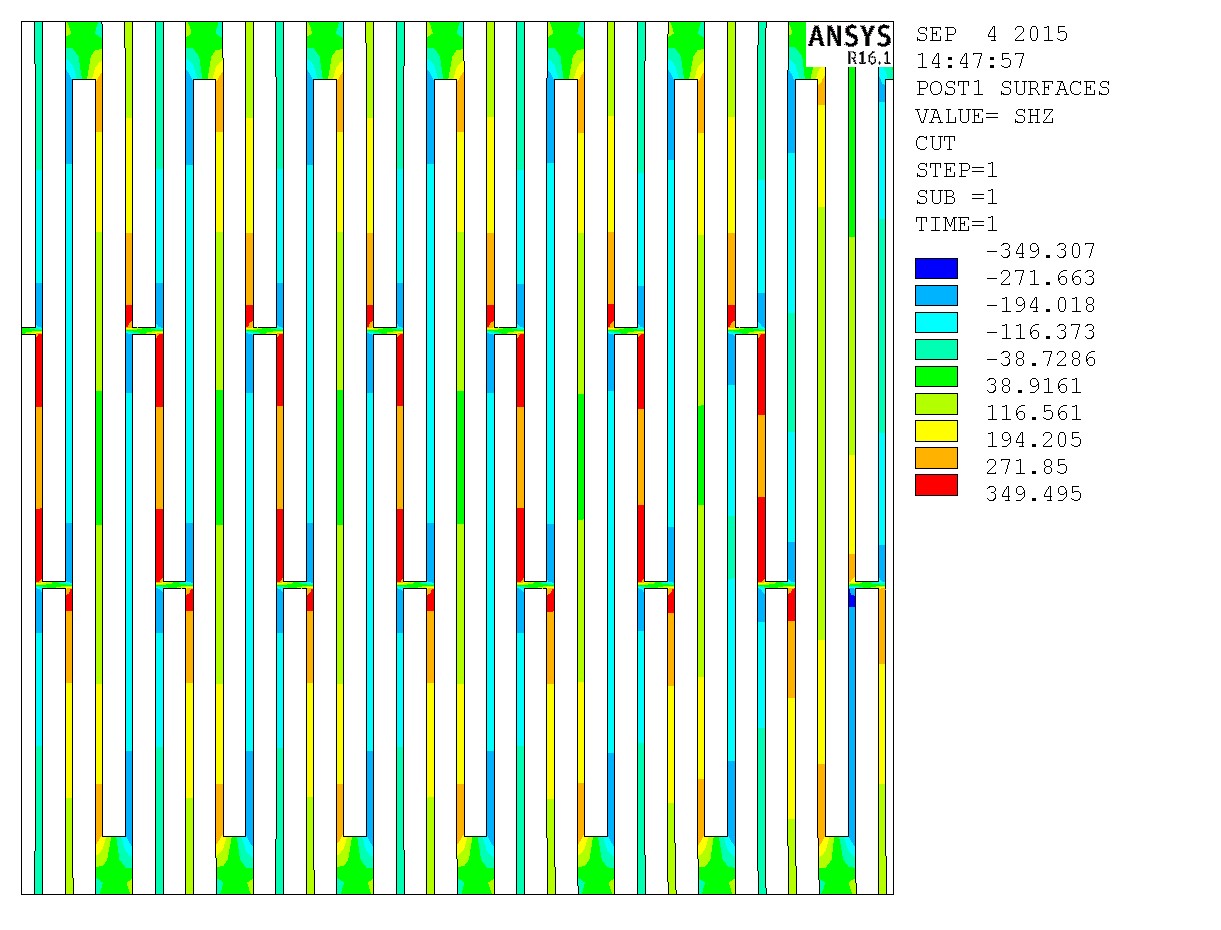
Pruebas de Propiedades del Caucho
¿De dónde viene la pérdida de energía en los transportadores? La investigación y la medición en el campo han demostrado que la indentación de resistencia a la rodadura (IRR en ingles) entre la correa y los rodillos puede representar ~ 60% de la pérdida de energía total (excluyendo el efecto de gravedad). Reducir la IRR es una forma efectiva de reducir el consumo de energía del transportador y la tensión de la correa. La IRR se debe a la pérdida de energía por histéresis de la deformación viscoelástica en la cubierta inferior de la correa, este factor esta estrechamente relacionado con las propiedades de la cubierta inferior de la correa. La correa de baja resistencia a la rodadura tiene una cubierta de goma modificada con menos pérdida de energía por histéresis, lo que puede reducir la demanda de energía del transportador entre 10% a 40% en comparación con la correa convencional. La banda transportadora LRR también es nombrada como correa de energía optimizada o correa de ahorro de energía por diferentes fabricantes.
CDI es pionero en la utilización de la correa LRR para optimizar el diseño del transportador con costos de capital y operación reducidos. Primero aplicamos esta tecnología en 1989 en el transportador terrestre Channar de 20 km en Australia, y nuestras últimas aplicaciones son en el sistema overland de Impumelelo de 27 km en Sudáfrica y el transportador tubular Yubei de 15 km en China.
Una pregunta clave es la medición de la propiedad IRR de un caucho en particular. CDI utiliza el Analizador mecánico dinámico (DMA) RSA3 de Rheometrics para medir las propiedades viscoelásticas E ‘(módulo elástico) y E “(módulo de pérdida) de una muestra de caucho en un amplio rango de temperatura, tensión y frecuencia. Los datos adquiridos de las pruebas DMA se procesan mediante un programa especial para generar curvas maestras y luego se incorporan al software Beltstat para los cálculos del transportador. Desde 1989 se viene desarrollando esta tecnología, aplicándola al diseño del transportador y acumulando datos de verificación.
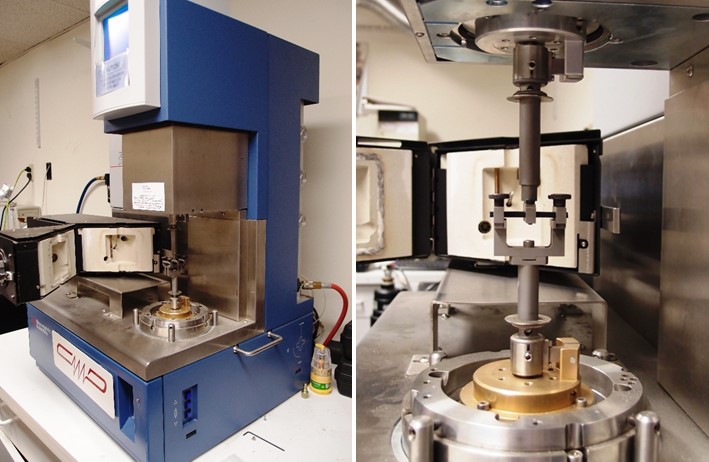
Correas Estándar
El software Beltstat proporciona un análisis muy detallado sobre la correa para la ingeniería del sistema. Incluye análisis de curvas verticales, curvas horizontales, rotación plana, transiciones de correa, flapping de correa (vibración) e índice de presión en los rodillos. El cálculo del índice de presión entre rodillos también es una tecnología patentada. Además, desarrollamos modelos especiales de elementos finitos para analizar casos únicos y obtener una visión más profunda del comportamiento de la correa de canal.
La siguiente figura muestra el FEA de una correa. La presión entre rodillos se refiere a la zona de la correa ubicad entre el rodillo central y el rodillo de lateral. Si la flexión es demasiado severa, la goma de la cubierta inferior puede fallar.
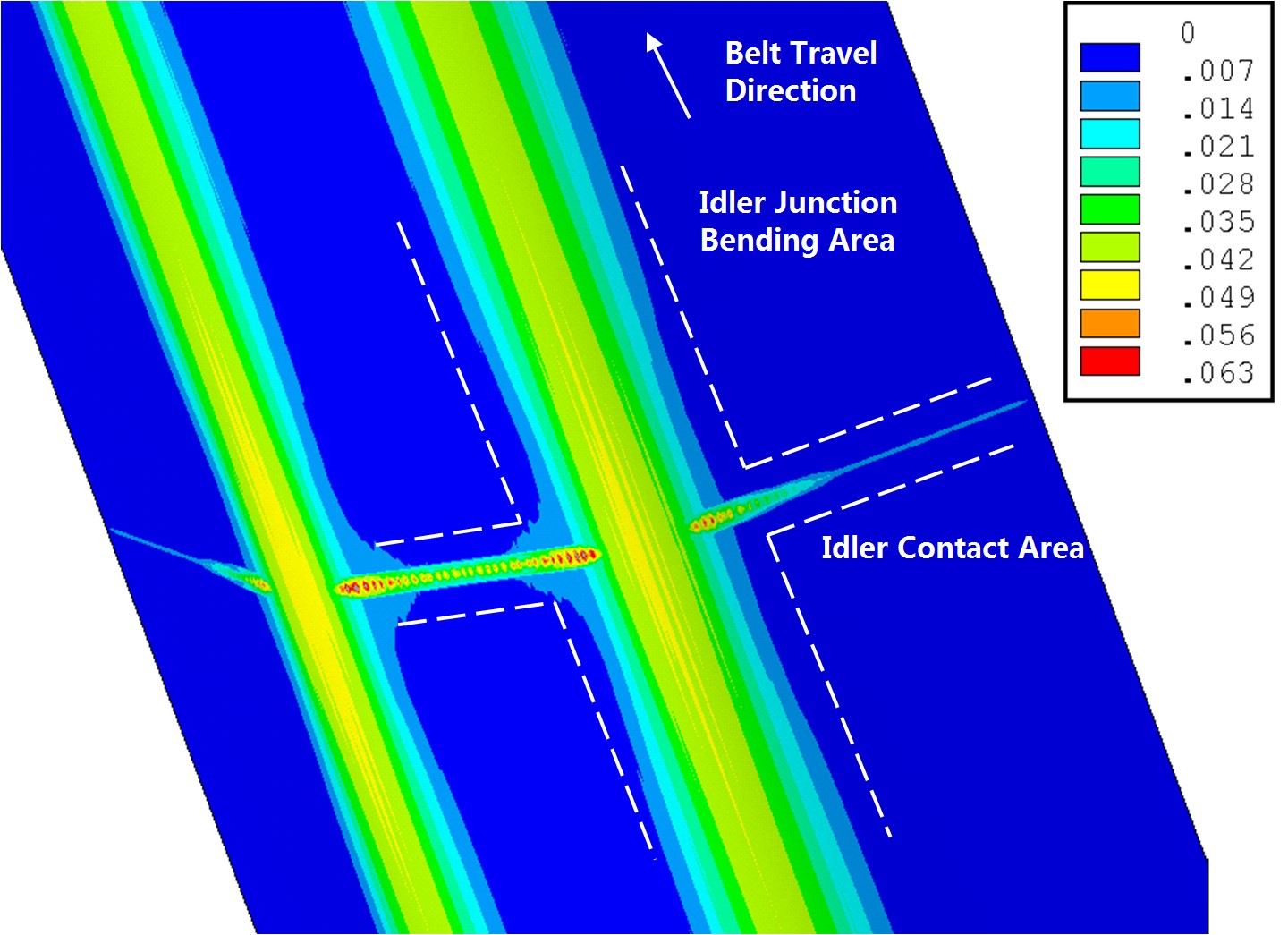
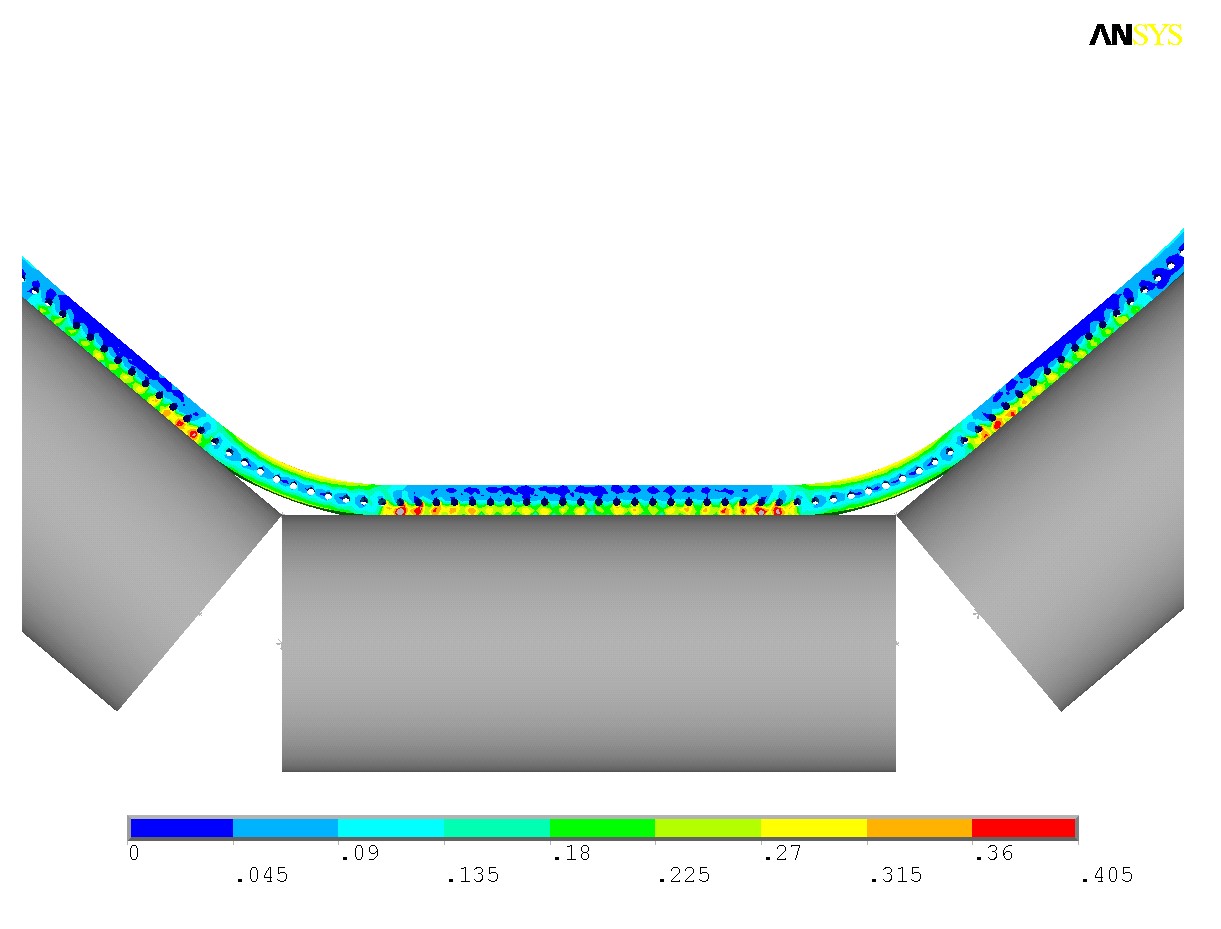
Tensión en la sección transversal del transportador a través del análisis de elementos finitos
El FEA también puede simular el comportamiento de la correa del canal en la curva horizontal, especialmente cuando hay una disposición de rueda libre especial (5 rodillos o canal profundo), un pequeño radio de curva horizontal o una banda especial.
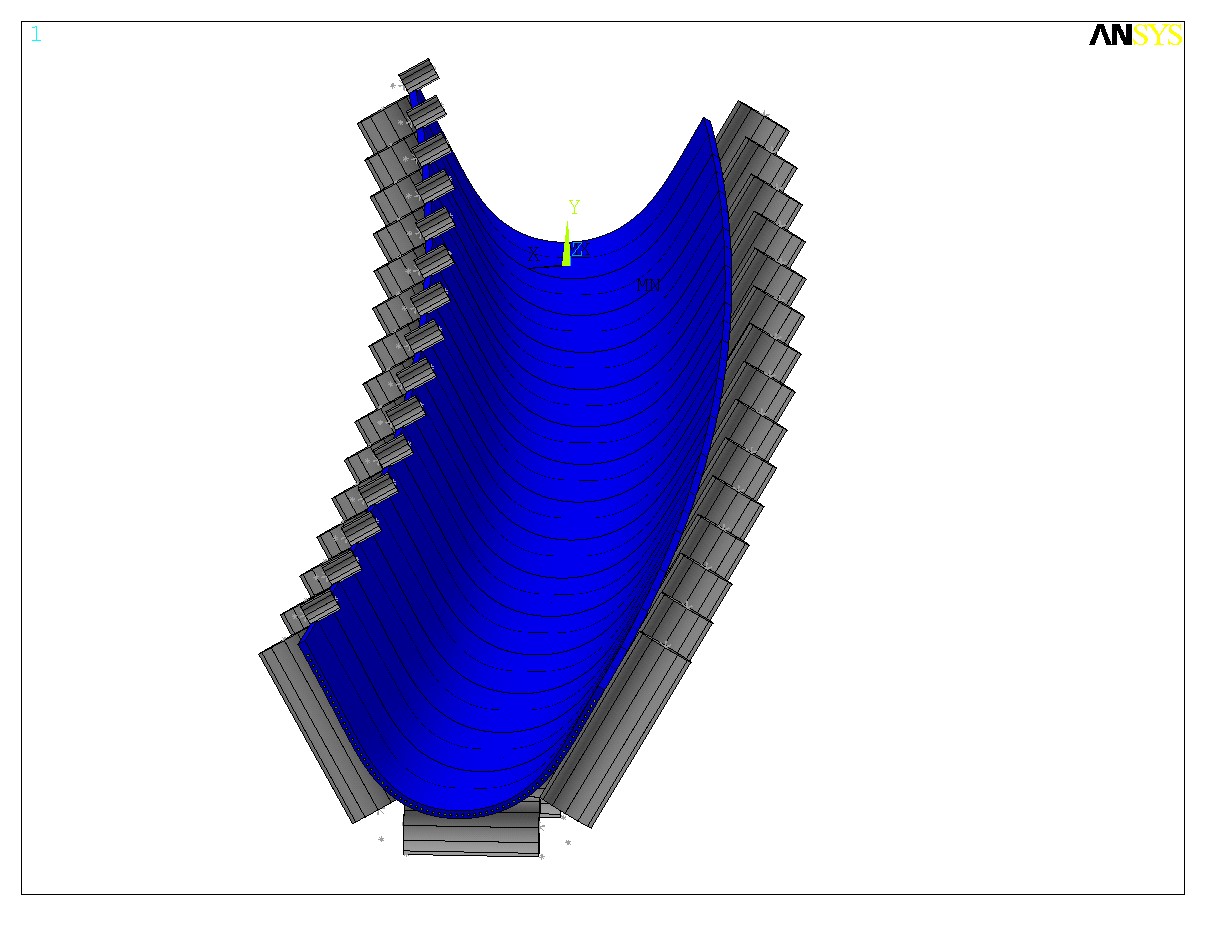
Correa Tubular
La cinta transportadora tubular tiene una influencia mucho mayor en el rendimiento del sistema de transporte que una correa estandar. El factor principal es la rigidez de la correa tubular, ya que a medida que la correa se enrolla en forma de tubo desde la forma plana, la rigidez intrínseca a la flexión de la correa se convierte en la presión de contacto en los rodillos circundantes. Una mayor rigidez de la correa dará como resultado una mayor presión de contacto. Esto le da a la correa tubular mayor estabilidad, mejor resistencia a la torsión y colapso durante las curvas horizontales y verticales. Pero la penalización es un mayor consumo de energía, una mayor tensión de la correa y la necesidad de una correa más fuerte y un mayor tamaño de transmisión. Desde el punto de vista del diseño, hay un equilibrio en la rigidez de la correa para lograr para cada proyecto individual. Si la ruta del transportador es recta, no hay necesidad de diseñar una correa tubular con alta rigidez. Se puede lograr un menor consumo de energía y costo de capital. Si la ruta del transportador tiene muchas curvas con radios pequeños, la rigidez de la correa debe aumentarse en consecuencia para acomodar el efecto de flexión de las curvas, de modo que la correa no tenga rotación, torsión y colapso excesivos.
CDI utiliza la prueba de flexión de tres puntos para medir la rigidez de la correa de la tubería y calibrar las propiedades del material en el modelo de elementos finitos de la correa tubular. La flexión de tres puntos es una prueba de flexión bien definida. En comparación con la prueba de rigidez de seis puntos, es mucho más fácil hacer muestras de prueba y generar una base de datos de diseño. Una vez que se establecen buenas correlaciones numéricas y experimentales entre la rigidez a la flexión de tres puntos y la rigidez de la correa del tubo de seis puntos, no es necesario hacer muestras de correa de ancho completo y pasar por un proceso de prueba y error para cada diseño antes de la producción real de la correa.
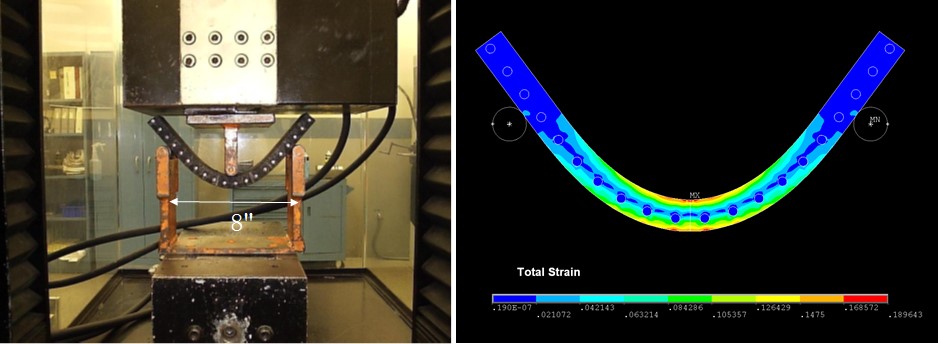
A diferencia de otros FEA publicados, donde se utilizan elementos de carcasa o sólidos simplificados para representar tanto materiales de caucho, cordón de acero y tela, CDI utiliza un modelo de correa tubular 3D completo donde las capas de caucho, cables de acero y tela se modelan individualmente con sus propias propiedades materiales. El comportamiento general de flexión de la correa tubular en FEA se compara y calibra con resultados de pruebas de rigidez de flexión de tres puntos y seis puntos. Desde el modo de elementos finitos, se puede obtener la presión de contacto en 6 rodillos circundantes. Combinando los resultados de la prueba de reología del caucho y la presión de contacto, se puede calcular la IRR de la correa del tubo para cada correa y transportador. Este es un enfoque más fundamental que los métodos empíricos basados en un factor de fricción DIN predefinido. Esto permite la optimización de la correa tubular mediante el uso de LRR y correas especiales como las correas tubulares de EPDM resistentes al calor.
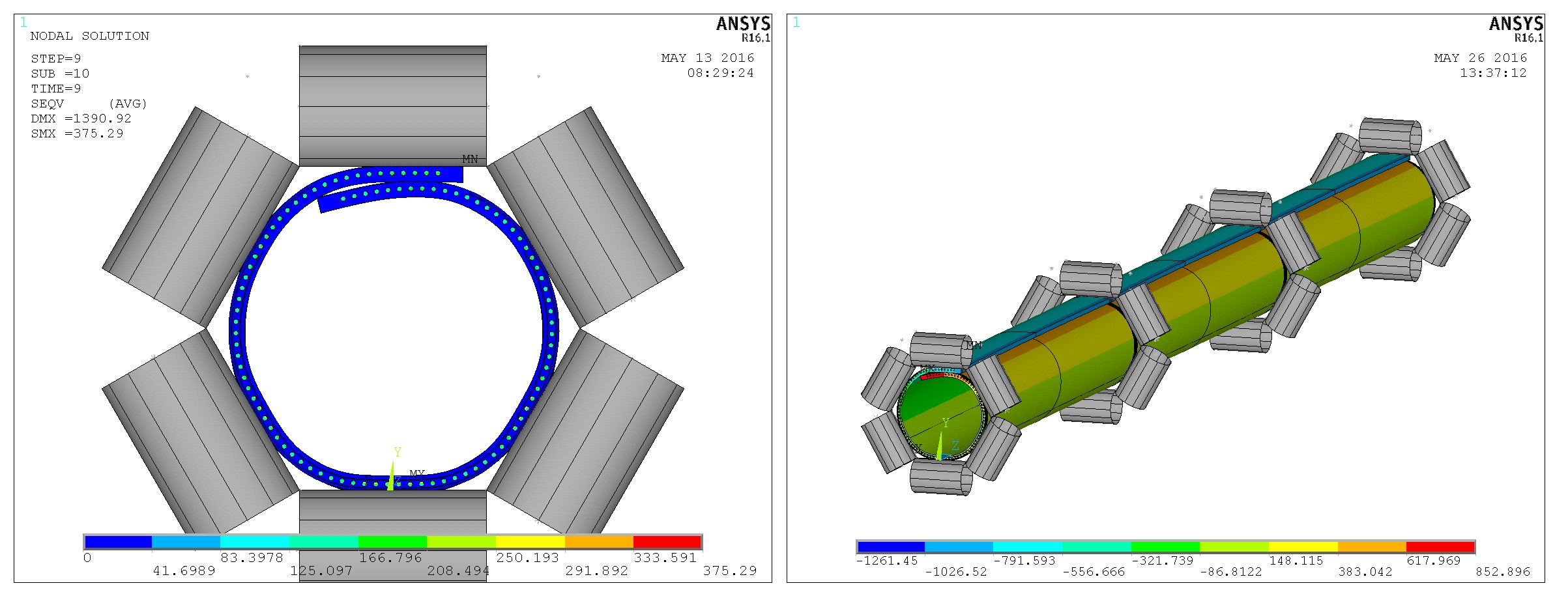
CDI diseñó una máquina de prueba de correa tubular a gran escala. La máquina de prueba tiene 11.4 m de largo, puede acomodar diámetros de tubería de 200 mm a 800 mm. Tiene un cilindro hidráulico en un extremo para aplicar tensión a la correa de prueba. Los paneles intermedios pueden ajustar la posición para simular curvas horizontales y verticales. Hay un panel donde las celdas de carga están unidas a 6 rodillos locos para medir las fuerzas de contacto. El proyecto es una colaboración con Double Arrow Rubber Co., Ltd., donde se encuentra la máquina de prueba.
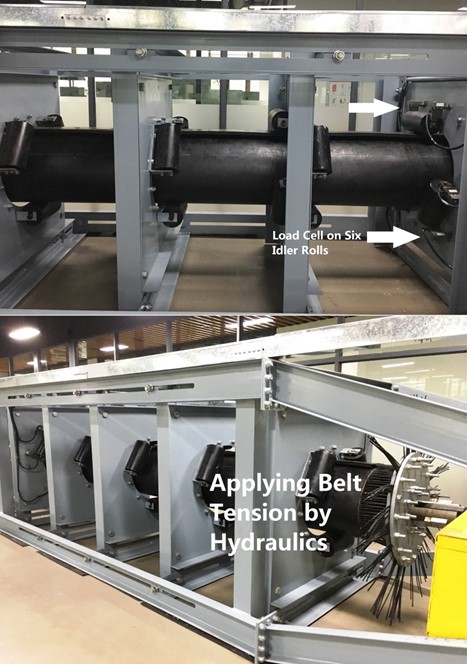
Cables de Acero Rotos
El problema de los cables de acero rotos en la correa transportadora es complicado. Hay muchas variables a considerar, por ejemplo, el número de cables rotos, la ubicación de los cables rotos, los diferentes ángulos de la correa, la transición, etc. La regla general convencional sobre los cables de acero rotos en la correa transportadora es que si hay menos del 5% de cables rotos en el borde de la correa y 10% de cables rotos en el centro de la correa, la correa se puede reparar sin volver a empalmar. Si el número de cables rotos excede este límite, la correa debe volver a empalmarse. La reparación típica llena la región de punción de la correa con goma. También se pueden insertar secciones de cables de acero en la región de punción. Sin embargo, la reparación no restablece la pérdida de la capacidad de transporte de tensión de los cables de acero rotos en la correa. Simplemente evita que el material se derrame a través de la región perforada. CDI desarrolló un programa para estudiar los cables rotos en las cintas transportadoras. Es una herramienta para aconsejar a los operadores de transportadores si deben reparar, volver a empalmar o hacer funcionar el transportador a menor capacidad para mantener el factor de seguridad de la correa. También se utiliza para hacer análisis de fallas donde los cables rotos en la cinta transportadora conducen a una rotura repentina de la correa.
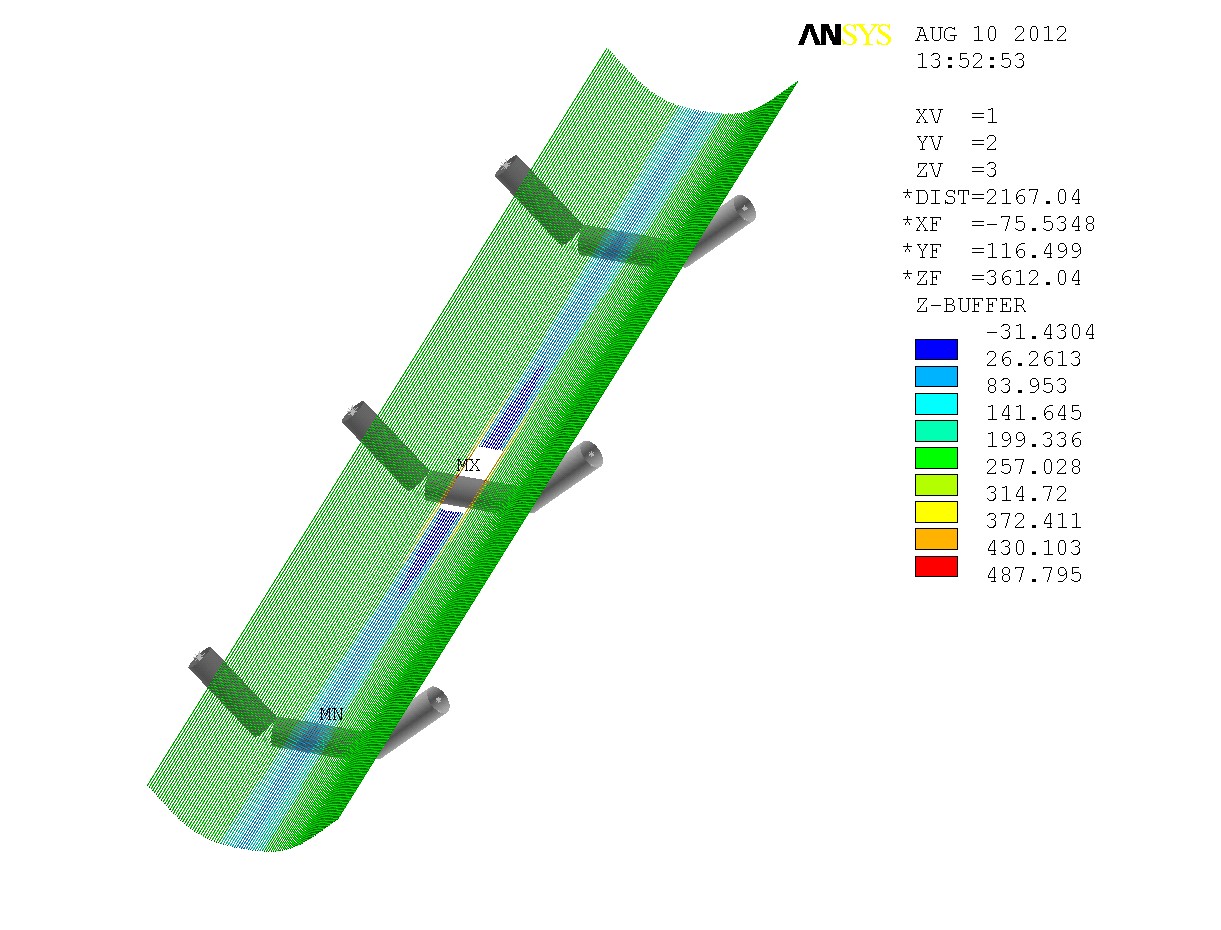